Difference between revisions of "F14: Self Driving Undergrad Team"
Proj user8 (talk | contribs) (→Project Video) |
Proj user8 (talk | contribs) (→Grading Criteria) |
||
(2 intermediate revisions by 2 users not shown) | |||
Line 1: | Line 1: | ||
− | |||
− | |||
− | |||
− | |||
− | |||
− | |||
− | |||
− | |||
− | |||
− | |||
− | |||
== Chi Lam == | == Chi Lam == | ||
<center> | <center> | ||
Line 55: | Line 44: | ||
| - Overall vehicle logic<br/>- Overall software vehicle Integration<br/>- CAN TX/RX messages architecture | | - Overall vehicle logic<br/>- Overall software vehicle Integration<br/>- CAN TX/RX messages architecture | ||
| - Vehicle hardware interfacing<br/>- Assistant to other teams<br/>- Module specific logic | | - Vehicle hardware interfacing<br/>- Assistant to other teams<br/>- Module specific logic | ||
− | | - Module specific logic<br/>- CAN RX processing | + | | - Module specific logic<br/>- CAN RX processing<br/>- GPS waypoint logic |
|- | |- | ||
|} | |} | ||
Line 2,623: | Line 2,612: | ||
=== Project Source Code === | === Project Source Code === | ||
− | * [https:// | + | * [https://gitlab.com/cpham/undergrad243/ GitLab Source Code Link] |
== References == | == References == |
Latest revision as of 19:43, 5 March 2015
Contents
- 1 Chi Lam
- 2 Self-Driving Autonomous Car
- 3 Abstract
- 4 Objectives & Introduction
- 5 We are
- 5.1 Schedule
- 5.2 Parts List & Cost
- 5.3 Design & Implementation
- 5.3.1 Hardware Design
- 5.3.2 Sensor Controller Team Hardware Design
- 5.3.3 Motor Controller Team Hardware Design
- 5.3.4 I/O Team Hardware Design
- 5.3.5 Communication Bridge + Android Hardware Design
- 5.3.6 Geographical Controller Team Hardware Design
- 5.3.7 Master Controller Team Hardware Design
- 5.3.8 Hardware Interface
- 5.3.9 Software Design
- 5.3.9.1 Sensor Controller Team Software Design
- 5.3.9.2 Motor Controller Team Software Design
- 5.3.9.3 Motor Movement Commands
- 5.3.9.4 I/O Team Software Design
- 5.3.9.5 Communication Bridge + Android Software Design
- 5.3.9.6 Geographical Controller Team Software Design
- 5.3.9.7 Master Controller Team Software Design
- 5.3.10 Software Interface
- 5.3.10.1 Sensor Controller Team Software Interface
- 5.3.10.2 Motor Controller Team Software Interface
- 5.3.10.3 I/O Team Software Interface
- 5.3.10.4 Communication Bridge + Android Software Interface
- 5.3.10.5 Geographical Controller Team Software Interface
- 5.3.10.6 Master Controller Team Software Interface
- 5.3.10.7 CAN Communication Table
- 5.4 Testing
- 5.5 Technical Challenges
- 5.6 Conclusion
- 5.7 References
Chi Lam
In Memory of Chi Lam
June 7th, 1991 - October 27th, 2014
This project is dedicated to Chi Lam, a beloved friend, dedicated Computer Engineering student, and member of this team.
You will be missed, friend
Self-Driving Autonomous Car
Abstract
The objective of the project is to create a self-driving autonomous car in a 15 person team. The car utilizes several components and sensors in order to get from Point A to Point B. Implementation of the car involves multiple SJONE processor boards using FreeRTOS to communicate with each other via CAN bus.
Objectives & Introduction
Team Members & Responsibilities
The team consisted of 15 undergraduate students taking a graduate level course, thus competing against the Master's level students.
We are
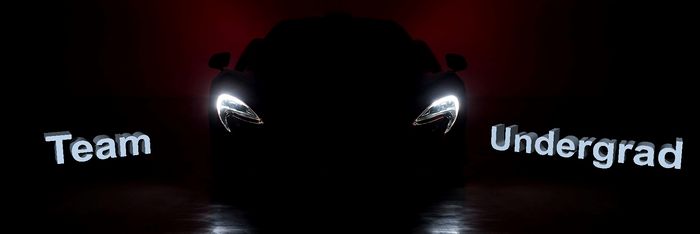
Master Controller Team | ||
---|---|---|
Charles Pham | Joshua Ambion | Michael Schneider |
- Overall vehicle logic - Overall software vehicle Integration - CAN TX/RX messages architecture |
- Vehicle hardware interfacing - Assistant to other teams - Module specific logic |
- Module specific logic - CAN RX processing - GPS waypoint logic |
Motor Controller Team | |
---|---|
Nikko Esplana | Chi Lam |
- Motor/steering control via PWM signals - interface/test/attach wheel encoder |
- Rest in peace Chi! |
Sensor Controller Team | |
---|---|
Sanjay Maharaj | Wei-chieh "Andy" Lo |
- Vehicle hardware - Sensor implementation - CAN communication |
- Sensor implementation - Sensor values verification - CAN communication |
Geographical Controller Team | ||
---|---|---|
Carlos Fernandez-Martinez | Zach Baumgartner | Albert Chen |
- Compass calibration/integration & structure modelling | - GPS testing/integration & structure modelling | - CAN communication |
Bridge Controller Team | ||
---|---|---|
Robert Julius | Tim Martin | Joseph Bourne |
- Android Application | - Bluetooth Message Interface | - Board to CAN Communication |
IO Controller Team | |
---|---|
Devin Villarosa | George Sebastian |
- Receive Task - GUI Interface - Headlights Task - uLCD Library |
- Event Handle Task - GUI Interface - Headlights Task - uLCD Library |
Schedule
Final Product Schedule
Week# | Date | Task | Actual |
---|---|---|---|
1 | 10/12 | CAN Network Benchtest | Complete |
2 | 10/15 | Basic CAN Communication | Complete |
3 | 10/31 | Secure devices to R/C car | Complete |
4 | 11/7 | Basic Vehicle Self-Driving Test | Complete |
5 | 11/14 | P2P testing and improved obstacle avoidance | Complete |
6 | 11/31 | Buffer time for previous tasks and increased vehicle speed | Complete |
Sensor Controller Schedule
Week# | Date | Task | Actual |
---|---|---|---|
1 | 10/13 | Sensor Input Distance Calibration | Incomplete: Need sensor value "filtering" logic. (Completed ~12/2) |
2 | 10/17 | Off car CAN network test (full team) | Completed. Able to send raw sensor value to master. |
3 | 10/20 | Interface Sensors with CAN | Completed. Updates to the formatting of data being sent is ongoing. |
4 | 10/27 | Mount Sensors and test coverage | Completed. Still need to mount with actual brackets. |
5 | 10/31 | Mount Sensors with 3d printed brackets | Completed. IR brackets to be printed based on offset. |
6 | 11/1 | Implement diagnostic LED patterns | Completed. |
7 | 11/3 | Send obstacle avoidance decisions to master | Completed. Raw values sent to master for processing. |
8 | 11/4 | Add RJ11 cabling to all sensors | Completed. Still need to make neat and tidy. |
9 | 11/10 | Eliminate outliers (software) | Completed. |
10 | 11/13 | Eliminate outliers by strengthening sensor wiring (hardware) | Completed. |
12 | 11/24 | Continue testing and tuning as necessary | Completed. |
Motor Controller Schedule
Week# | Date | Task | Actual |
---|---|---|---|
1 | 10/12 | Open up servo and motor modules,
find a speed sensor |
Complete |
2 | 10/19 | Interface/test PWM bus to steering servo and DC motor | Complete |
3 | 10/26 | Allow self-driving capability with master/bridge/sensor teams | Incomplete, only partial self-driving achieved |
4 | 11/2 | Improve fine motor movements with master/sensor teams | Incomplete, still needs tweaking. |
5 | 11/9 | Once wheel encoder comes in, learn/test/implement onto car | Incomplete, wheel encoder cannot be implemented, scrapping. |
6 | 11/16 | Integrate wheel encoder with rest of car | Incomplete, scrapped wheel encoder. |
7 | 11/23 | Test for proper operation | Complete, added functionality for center steer and forward speed calibration. |
8 | 11/30 | Continue testing until proper operation | Complete, motor works as intended. |
I/O Schedule
Week# | Date | Task | Actual |
---|---|---|---|
1 | 10/4 | Create LCD Screen Library (create ability to set value, get value, and write string to LCD screen) | 10/4 (String function completed on ~10/18) |
2 | 10/4 | Create LCD Screen GUI (generate forms for debugging and general usage) | 10/4 |
3 | 10/11 | LCD Library Test (Do unit tests on individual functions for LCD library)
Ability to get value from gauge on screen. Ability to set value to gauge on screen. Ability to send a string value to screen. |
10/11 (Finished string function on ~10/18) |
4 | 10/11 | Interface LCD with CAN
Create task for LCD event loop. Create task for Receiving on CAN. |
Complete (Completed on 10/26/2014) |
5 | 10/18 | Test LCD with CAN
Process CAN Messages from system |
Complete (Completed on 10/25/2014) |
6 | 10/25 | Implement onto Final Product | Complete (Completed on 11/23/2014) |
7 | 11/2 | Headlights for car (hardware and software) + Aesthetics for GUI + Clean up code | Complete (Completed on 12/01/2014) *NOTE Headlights are lost in hardware land |
Communication Bridge and Android Schedule
Week# | Date | Task | Actual |
---|---|---|---|
1 | 10/13 | CAN Network Test | Complete. |
2 | 10/20 | Interface Bluetooth Module with CAN | Complete. |
3 | 10/27 | Mount PCB on car | Complete. |
4 | 11/3 | Create basic Android application | Complete (completed ~10/18). |
5 | 11/10 | Add map onto the Android application | Complete (completed ~10/25). |
6 | 11/17 | Send/receive CAN Messages via Android Application | Complete (sending completed ~10/18, receiving ~11/1). |
7 | 11/24 | Debug and Optimize Android Application | Complete. |
8 | 12/1 | Continue Debugging and Optimizing as Necessary | Complete. |
Geographical Controller Schedule
Week# | Date | Task | Actual |
---|---|---|---|
1 | 10/8 | Interface with GPS/Compass | Complete - receiving values |
2 | 10/15 | Finish core API | Complete |
3 | 10/22 | GPS get fix and receive raw data | Complete - raw data received, but need faster fix |
4 | 10/22 | Compass determine heading | Complete - heading may require additional calibration |
5 | 10/29 | Implement calibration algorithm | Complete |
6 | 10/29 | GPS parse raw data to extract needed data | Complete - returns latitude, longitude, and calculated heading |
7 | 10/29 | Compass use heading from GPS to improve accuracy | N/A - Decided that magnetometer provides accurate enough reading |
8 | 11/5 | Improve GPS satellite procurement (antennae?) | Complete - attached antennae to GPS unit |
9 | 11/12 | Improve boot up time of GPS module via warm start | N/A - EZ start fast fix mode cannot coincide with 10 Hz update rate (defaults down to 1 Hz) |
10 | 11/12 | Fine tune compass calibration technique for accuracy | Complete - Compass still about 20 degrees off, but well within usable margins. Offset likely due to nearby power source on car. |
11 | 12/3 | Buffer time for completion of previous tasks | Complete |
Master Controller Schedule
Line Item # | Expected End Date | Task | Status |
---|---|---|---|
1 | 10/15/14 | Decide on raw CAN struct architecture | Early Completion |
2 | 10/18/14 | Develop and layout general common CAN messages | On-time Completion |
3 | 10/20/14 | Design vehicle initialization procedure | Early Completion |
4 | 10/23/14 | Develop and layout Inter-Controller Communication - Each Module's CAN messages | Early Completion |
5 | 10/25/14 | Design vehicle initial running freed drive mode procedure - Controlled via Phone, no object detection and avoidance, no GPS, no Heading | Early Completion |
6 | 10/28/14 | Complete design on vehicle running free drive mode procedure | On-time Completion |
7 | 10/30/14 | Design vehicle initial running indoor drive mode procedure - Timed autonomous drive , object detection and avoidance, (possibly heading), and no GPS | Late Completion |
8 | 11/01/14 | All CAN message definitions complete | Early Completion |
9 | 11/02/14 | Design vehicle initial running gps drive mode procedure - Full autonomous drive , object detection and avoidance, heading and GPS | Late Completion |
10 | 11/05/14 | All CAN message receive processing complete | On-time Completion |
11 | 11/14/14 | All basic vehicle functionality state machines implemented and verified | On-time Completion |
12 | 11/15/14 | Complete design on vehicle running indoor drive mode procedure | Late Completion |
13 | 11/20/14 | Complete design on vehicle running gps drive mode procedure | Late Completion |
14 | 11/30/14 | Any additional advanced functionality implemented and verified | Late Completion |
Parts List & Cost
Line Item# | Part Desciption | Vendor | Part Number | Qty | Cost ($) |
---|---|---|---|---|---|
1 | CAN Board | Waveshare International Limited | SN65HVD230 | 15 | 92.00 |
2 | Traxxas Slash Pro 2WD Short-Course R/C Truck | Traxxas | 58034 Slash | 1 | 337.00 |
3 | Adafruit Ultimate GPS Breakout | Adafruit | MTK3339 | 1 | 39.95 + (4.685 Shipping) |
4 | Triple-axis Accelerometer+Magnetometer (Compass) Board | Adafruit | LSM303 | 1 | 14.95 + (4.685 Shipping) |
5 | GPS Antenna - External Active Antenna - 3-5V 28dB 5 Meter SMA | Adafruit | 960 | 1 | 12.95 + (4.735 Shipping) |
6 | SMA to uFL/u.FL/IPX/IPEX RF Adapter Cable | Adafruit | 851 | 1 | 3.95 + (4.735 Shipping) |
7 | 3.5" Intelligent module w/ Touch | 4D Systems | uLCD 35DT | 1 | 89.00 |
8 | 2GB microSD Card | ||||
9 | uUSB-PA5 Programming Adaptor | ||||
10 | 150mm 5 way Female-Female jumper cable | ||||
11 | 5 way Male-Male adaptor | ||||
12 | Sharp Infrared Range Finder | 4D Systems | GP2Y0A21 | 2 | 9.95 + 3.32 Shipping |
13 | SainSmart Sonar Ranging Detector | Amazon | HC-SR04 | 3 | 5.59 |
14 | RC LED Headlights | Amazon Prime | 2 | 5.99 | |
15 | XBee Bluetooth | Amazon Prime | WLS04051P | 1 | 27.50 |
16 | SJONE Board | Preet Industries | 6 | 480.00 | |
17 | Traxxas XL5 ESC unit | dollarhobbyz.com | 2WDS ESC | 2 | 54.00 + (4.67 Shipping) |
Additional Shipping | $0.00 | ||||
Total Cost | $1199.66 |
Design & Implementation
Hardware Design
Overall Hardware Design Components
58034 Traxxas Slash RC Truck:
|
|
SN65HVD230 CAN Board Transceiver:
|
|
3D Printed Materials:
The first structure that was built was the main platform. This platform acted as a mount for the six SJOne boards and the six CAN transceivers. Then, several structures needed to be created to mount the ultrasonic and sonar sensors at the front and back of the vehicle. Next, the LCD required a mount so it could float freely on the car and be both usable and sturdy, in case of a crash. Finally, a tower was designed to keep the antennae high and away from other components, like the magnometer. This is because the antennae has a huge magnet on the bottom for mounting purposes and was interfering with the compass readings. The models of the different structures can be seen in this section.
|
Sensor Controller Team Hardware Design
Sensor Pin Connections
Line Item# | Node A Source | Node A Pin | Node B Source | Node B Pin | Description |
---|---|---|---|---|---|
1 | 3.3V Power Supply | 3.3V | SJOne Board | 3V3 | SJOne Power |
2 | 3.3V Power Supply | GND | SJOne Board | GND | SJOne Ground |
3 | CAN Transceiver | Tx | SJOne Board | P0.1 (Tx) | SJOne - CAN Tx |
4 | CAN Transceiver | Rx | SJOne Board | P0.0 (Rx) | SJOne - CAN Rx |
5 | CAN Transceiver | 3.3V | 3.3V Power Supply | 3.3V | SJOne - CAN Power |
6 | CAN Transceiver | Ground | 3.3V Power Supply | GND | SJOne - CAN Ground |
7 | HC-SR04 Ultrasonic Sensor (Front Left) | Vcc | 5V Power Supply | +5V | Front Left Sensor Power |
8 | HC-SR04 Ultrasonic Sensor (Front Left) | GND | 5V Power Supply | GND | Front Left Sensor GND |
9 | HC-SR04 Ultrasonic Sensor (Front Left) | Echo | SJOne Board | P2.0 | Front Left Sensor Echo |
10 | HC-SR04 Ultrasonic Sensor (Front Left) | Trig | SJOne Board | P2.1 | Front Left Sensor Trig |
11 | HC-SR04 Ultrasonic Sensor (Front Right) | Vcc | 5V Power Supply | +5V | Front Right Sensor Power |
12 | HC-SR04 Ultrasonic Sensor (Front Right) | GND | 5V Power Supply | GND | Front Right Sensor GND |
13 | HC-SR04 Ultrasonic Sensor (Front Right) | Echo | SJOne Board | P2.2 | Front Right Sensor Echo |
14 | HC-SR04 Ultrasonic Sensor (Front Right) | Trig | SJOne Board | P2.3 | Front Right Sensor Trig |
15 | LV-MaxSonar-EZ-0 Ultrasonic Range Sensor (Front Middle) | Vcc | 5V Power Supply | +5V | Front Middle Sensor Power |
16 | LV-MaxSonar-EZ-0 Ultrasonic Range Sensor (Front Middle) | GND | 5V Power Supply | GND | Front Middle Sensor GND |
17 | LV-MaxSonar-EZ-0 Ultrasonic Range Sensor (Front Middle) | Echo | SJOne Board | P2.4 | Front Middle Sensor Echo |
18 | LV-MaxSonar-EZ-0 Ultrasonic Range Sensor (Front Middle) | Trig | SJOne Board | P2.5 | Front Middle Sensor Trig |
19 | HC-SR04 Ultrasonic Sensor (Rear Left) | Vcc | 5V Power Supply | +5V | Rear Left Sensor Power |
20 | HC-SR04 Ultrasonic Sensor (Rear Left) | GND | 5V Power Supply | GND | Rear Left Sensor GND |
21 | HC-SR04 Ultrasonic Sensor (Rear Left) | Echo | SJOne Board | P2.6 | Rear Left Sensor Echo |
22 | HC-SR04 Ultrasonic Sensor (Rear Left) | Trig | SJOne Board | P2.7 | Rear Left Sensor Trig |
23 | HC-SR04 Ultrasonic Sensor (Rear Right) | Vcc | 5V Power Supply | +5V | Rear Right Sensor Power |
24 | HC-SR04 Ultrasonic Sensor (Rear Right) | GND | 5V Power Supply | GND | Rear Right Sensor GND |
25 | HC-SR04 Ultrasonic Sensor (Rear Right) | Echo | SJOne Board | P2.8 | Rear Right Sensor Echo |
26 | HC-SR04 Ultrasonic Sensor (Rear Right) | Trig | SJOne Board | P2.9 | Rear Right Sensor Trig |
27 | CAN Transceiver | CANL | CAN BUS | CANL | CANL to CAN BUS |
28 | CAN Transceiver | CANR | CAN BUS | CANR | CANR to CAN BUS |
Sensor Controller Hardware Design Components
HC-SR04 Ultrasonic Distance Sensor:
The HC-SR04 is a distance sensor which detects objects using ultrasonic signals. The sensor is capable of detecting distances within 2cm-500cm. The sensor runs off 5V DC. Four pins are used: Vcc, Ground, Trig, and Echo. These sensors are relatively inexpensive, so four sensors were purchased. The four HC-SR04 sensors were implemented on our car at the following locations: front-left, front-right, rear-left, and rear-right. |
|
LV-MaxSonar-EZ0 Ultrasonic Range Sensor:
|
Method of Operation
1. INPUT: The sensor is triggered by a 10uS pulse HIGH on the trig pin.
2. RANGING: The sensor sends out eight 40kHz sonar pulses.
3. OUTPUT: The sensor outputs a pulse HIGH with the pulse time depending on the distance of the object on the echo pin.
The the output from the echo pin can be seen below, as captured by an oscilloscope.
Motor Controller Team Hardware Design
As seen above, the car battery(accepts compatible Ni-MH, Li-Po, and Ni-Cad batteries) powers the ESC unit (XL-5), which in turn drives the Titan 12T-550 motor and also powers the steering servo. It is necessary for the ESC unit, steering servo and SJ One board to share a common ground in order for the PWM signals to have the same reference voltage.
The CAN transceiver requires the use of the SJ One Board's +3.3V and GND, as well as P0.0 (CAN RX) and P0.1 (CAN TX).
P2.0/P2.1 (PWM1/PWM2) controls the steering/motor via the SJ One board by sending out PWM signals that change the width of a 20ms period waveform. 1ms width represents a 0% duty cycle, 1.5ms width represents a 50% duty cycle, and 2ms width represents a 100% duty cycle.
Controlling motor and steering
In the photo above, a digital oscilloscope probes a PWM pin on the SJ One board and detects a signal with a 3.3 peak-to-peak voltage, a 100hz PWM frequency, and a width of 1.5ms (50% duty cycle). In terms of steering control, a width between 1ms to 1.499ms equates to left steering (1ms = max left angle) and a width between 1.501ms to 2ms equates to right steering (2ms = max right angle). The motor is similar, such that a width between 1ms to 1.499ms equates to a reverse throttle and a width between 1.501ms to 2ms equates to a forward throttle. For both steering and motor control, 1.5ms (50% duty cycle) represents a center steer or non-throttle.
Motor Controller Hardware Design Components
58034 Traxxas Slash RC Truck:
|
|
Traxxas XL-5 Electronic Speed Control (ESC) Unit:
|
|
Steering Servo:
|
Motor Pin Connections
Line Item# | Node A Source | Node A Pin | Node B Source | Node B Pin | Description |
---|---|---|---|---|---|
1 | 3.3V Power Supply | 3.3V | SJOne Board | 3V3 | SJOne Power |
2 | 3.3V Power Supply | GND | SJOne Board | GND | SJOne Ground |
3 | CAN Transceiver | CAN Tx | SJOne Board | P0.1 (Tx) | SJOne - CAN Tx |
4 | CAN Transceiver | CAN Rx | SJOne Board | P0.0 (Rx) | SJOne - CAN Rx |
5 | CAN Transceiver | 3.3V | 3.3V Power Supply | 3.3V | SJOne - CAN Power |
6 | CAN Transceiver | Ground | 3.3V Power Supply | GND | SJOne - CAN Ground |
7 | CAN Transceiver | CANL | CAN BUS | CANL | CANL to CAN BUS |
8 | CAN Transceiver | CANR | CAN BUS | CANR | CANR to CAN BUS |
9 | Steering Servo | PWM Port | SJOne Board | P2.0 PWM | Steering Control |
10 | Steering Servo | Ground | SJOne Board | GND | Common ground for reference voltage |
11 | ESC/Motor | PWM Port | SJOne Board | P2.1 PWM | Motor Control |
12 | ESC/Motor | Ground | SJOne Board | GND | Common ground for reference voltage |
I/O Team Hardware Design
I/O Design Components
uLCD-35DT Intelligent Display Module:
|
I/O Pin Connections
Line Item# | Node A Source | Node A Pin | Node B Source | Node B Pin | Description |
---|---|---|---|---|---|
1 | LCD | 1 (LCD +5V) | 5V Power Supply | 5V | uLCD 35DT LCD Power |
2 | LCD | 7 (LCD GND) | 5V Power Supply | GND | uLCD 35DT LCD Ground |
3 | LCD | 5 (LCD RX) | SJOne Board | RX3 | uLCD 35DT LCD Receive Pin |
4 | LCD | 3 (LCD TX) | SJOne Board | TX3 | uLCD 35DT LCD Transmit Pin |
5 | 3.3V Power Supply | +3.3V | SJOne Board | 3V3 | SJOne Power |
6 | 3.3V Power Supply | GND | SJOne Board | GND | SJOne Ground |
7 | UART2 RX | P2.9 | SJOne RX | ||
8 | UART2 TX | P2.8 | SJOne TX | ||
9 | +5V | +5V Power | SJOne Board | GPIO P2.0 | Active Low |
10 | +5V | +5V Power | SJOne Board | GPIO P2.1 | Active Low |
11 | +5V | +5V Power | SJOne Board | GPIO P2.2 | Active Low |
12 | +5V | +5V Power | SJOne Board | GPIO P2.3 | Active Low |
13 | CAN Transceiver | CAN Tx | SJOne Board | P0.1 (Tx) | SJOne - CAN Tx |
14 | CAN Transceiver | CAN Rx | SJOne Board | P0.0 (Rx) | SJOne - CAN Rx |
15 | CAN Transceiver | CAN 3.3V | 3.3V Power Supply | 3.3V | SJOne - CAN Power |
16 | CAN Transceiver | CAN Ground | 3.3V Power Supply | GND | SJOne - CAN Ground |
17 | CAN Transceiver | CANL | CAN BUS | CANL | CANL to CAN BUS |
18 | CAN Transceiver | CANR | CAN BUS | CANR | CANR to CAN BUS |
Communication Bridge + Android Hardware Design
The Bluetooth module is connected to the SJOne board through the XBee socket, with only the RX/TX data connections into the board.
Communication Bridge Pin Connections
Line Item# | Node A Source | Node A Pin | Node B Source | Node B Pin | Description |
---|---|---|---|---|---|
1 | 3.3V Power Supply | 3.3V | SJOne Board | 3V3 | SJOne Power |
2 | 3.3V Power Supply | GND | SJOne Board | GND | SJOne Ground |
3 | CAN Transceiver | CAN Tx | SJOne Board | P0.1 (Tx) | SJOne - CAN Tx |
4 | CAN Transceiver | CAN Rx | SJOne Board | P0.0 (Rx) | SJOne - CAN Rx |
5 | CAN Transceiver | CAN 3.3V | 3.3V Power Supply | 3.3V | SJOne - CAN Power |
6 | CAN Transceiver | CAN Ground | 3.3V Power Supply | GND | SJOne - CAN Ground |
7 | Bluetooth Bee | VCC | 3.3V Power Supply | 3V3 | Bluetooth Bee Power |
8 | Bluetooth Bee | GND | 3.3V Power Supply | GND | Bluetooth Bee GND |
9 | Bluetooth Bee | RX | SJOne Board | P2.9 (RXD2) | Bluetooth Bee RX |
10 | Bluetooth Bee | TX | SJOne Board | P2.8 (TXD2) | Bluetooth Bee TX |
11 | CAN Transceiver | CANL | CAN BUS | CANL | CANL to CAN BUS |
12 | CAN Transceiver | CANR | CAN BUS | CANR | CANR to CAN BUS |
Communication Bridge + Android Hardware Design Components
Bluetooth Bee Standalone:
The Bluetooth Bee Standalone Module by Seeed Studio Works allows for the connection of a bluetooth module onto the XBee Socket of the SJOne Board. This module contains an ATMEGA168 for reprogramming. Only the SJOne Board's UART2/3 pins are capable of transferring data to the module, depending on which UART the XBee Socket is connected to with a switch configuration. |
Geographical Controller Team Hardware Design
Geographical Pin Connections
Line Item# | Node A Source | Node A Pin | Node B Source | Node B Pin | Description |
---|---|---|---|---|---|
1 | 3.3V Power Supply | 3.3V | SJOne Board | 3V3 | SJOne Power |
2 | 3.3V Power Supply | GND | SJOne Board | GND | SJOne Ground |
3 | CAN Transceiver | Tx | SJOne Board | P0.1 (Tx) | SJOne - CAN Tx |
4 | CAN Transceiver | Rx | SJOne Board | P0.0 (Rx) | SJOne - CAN Rx |
5 | CAN Transceiver | 3.3V | 3.3V Power Supply | 3.3V | SJOne - CAN Power |
6 | CAN Transceiver | Ground | 3.3V Power Supply | GND | SJOne - CAN Ground |
7 | MTK3339 GPS | VCC | 5V Power Supply | +5V | MTK3339 GPS Power |
8 | MTK3339 GPS | GND | 5V Power Supply | GND | MTK3339 GPS GND |
9 | MTK3339 GPS | RX | SJOne Board | RXD2 | MTK3339 GPS RX |
10 | MTK3339 GPS | TX | SJOne Board | TXD2 | MTK3339 GPS TX |
7 | LSM303 Compass + Accelerometer | VIN | 5V Power Supply | +5V | Compass + Accelerometer Power |
8 | LSM303 Compass + Accelerometer | GND | 5V Power Supply | GND | Compass + Accelerometer GND |
9 | LSM303 Compass + Accelerometer | RX | SJOne Board | RXD2 | Compass + Accelerometer SCL |
10 | LSM303 Compass + Accelerometer | TX | SJOne Board | TXD2 | Compass + Accelerometer SDA |
11 | CAN Transceiver | CANL | CAN BUS | CANL | CANL to CAN BUS |
12 | CAN Transceiver | CANR | CAN BUS | CANR | CANR to CAN BUS |