S15: MENL (Monster Encounter Night Light)
Contents
Grading Criteria
- How well is Software & Hardware Design described?
- How well can this report be used to reproduce this project?
- Code Quality
- Overall Report Quality:
- Software Block Diagrams
- Hardware Block Diagrams
- Schematic Quality
- Quality of technical challenges and solutions adopted.
MENL (Monster Encounter Night Light)
Abstract
The monster encounter night light will have every single LED on when no motion is detected and no one is within distance of MELN. If someone is approaching MELN, depending on the distance of the object detected, The LED matrix will change into a pair of close eyes or a pair of open alert eyes.
Introduction
The MENL (Monster Encounter Night Light) is a children toy that will display multiple displays on the LED Matrices depending on the location and movement of objects around it. Once MENL had been turn on, the LED matrices will turn all on and dispay a bright white light to simulate a night light that children who are scared of the dark use. If some one is moving around MENL farther then 40 cm, The motion sensor will detect the presence of the moving object and the LED matrices will turn off and switch to the Display of two closed eyes, this simulates the change from night light form to Encounter mode. Once the moving object gets closer between the boundaries of the Distance Sensor, it will change the display to an alert MENL by having its eyes wide open and the color of the eyes change to yellow to emote a warning color.
Objectives
List of Objects to be completed:
1. Distance Sensor Interface
2. Motion Sensor Interface
3. Servo, skeleton rotation(cancelled)
4. LED Matrix SPI Interface
5. LCD Display I2C Interface (cancelled)
6. Communication between Sensors
7. Display result in LED Matrix
Team Members
- Moises Quinteros
- William Hernandez
Schedule
Week# | Date | Task | Actual | |
---|---|---|---|---|
1 | 4/13 | Order all required parts for project. | Completed, parts should arrive in a couple of weeks. | |
2 | 4/20 | Research on Sensors and work on overall design. | Completed. | |
3 | 4/27 | Research on Motion and Distance sensor and work on them functioning individually. | Completed, Problems Encountered= Motion Sensor seems to have a timing issues, responding late to motion. Distance sensor needs
an equation to translate the values obtain to centimeters. | |
4 | 5/4 | Buy extra LED Matrix, work on LCD display and LED Matrix display. | Completed: no. Problems Encountered: LCD display datasheets does not have the correct Slave Address,
we are working on it. LED Matrix doesnt seem to be displaying correct send Byte. | |
5 | 5/11 | Work on Skeleton and putting everything together. | Completed: Half Problems Encountered: LED was fixed, LCD Display does not want to work with correct Slave Address. | |
6 | 5/18 | Test, finish anything not yet completed. | Completed: half Problems Encountered: Drop LCD as it wasnt working and drop servo as it was unpredictable and would sometimes spin wildly. |
Parts List & Cost
Item# | Desctiption# | Price# |
---|---|---|
Motion Sensor | PIR Motion Sensor (JST)
SEN-13285 |
$9.95 |
Distance Sensor | Infrared Proximity Sensor - Sharp GP2Y0A21YK | $13.95 |
LED Matrices | 2 MOD-LED8x8RGB | $30.50 ea |
Cables | Female and Male jumper wires | $8 |
SJ_One Board | SJ_One Board | $80 |
Bread Board | Regular bread board | $5 |
Capacitors, resistors , and other components | Multiples items for pull up resistors, power supply and other needs. | varies |
Skeleton Components | Styro foam, Small Coasters, Screws, Super Glue | $35~ |
Design & Implementation
Hardware Design
BLOCK Diagram: The representation of the given block diagram influences the structure under which the embedded system was created. Two primary eight by eight light emitting diode displays exist for logical representation of action event when a person or thing sensed with respect to the motion sensor block. The distance sensor block is just a module to represent the measure distance with respect to a specific voltage as the the embedded board uses analog to digital functionality in order to calculate the given distance from an approaching source.
DISTANCE VS VOLTAGE GRAPH By staring to take different distances from voltages using a ruler and a white paper with proper inputs connected as shown in block diagram, a graph was created. The intention was that as inputs were taken an output needed to be predicted at which voltage a distance could be read. The table that is shown demonstrates the findings. The equation in the graph is a formal description of the distance sensing unit behavior.
Hardware Interface
For the parts required to complete our project, we opted on using GPIO for the motion sensor since we only needed to read a high and low signal from it to know if anyone was approaching MENL. The distance sensor provided us with an analog output which lead us the analog to digital libraries provided in FreeRtos. For the LED matrices, we tested it using the spi 1 library as well as we created our own SPI driver from our previous lab assigments. Both of them work exactly the same. Since the board came with a Pic device, all we needed to do was to send the correct byte through SPI. In addition, we needed a chip select to enable the output for the registers controlling the matrices. We used a GPIO signal for this. Similar to the SPI part, we used our own drivers, but decided to use the libraries to reduce the amount of code. All of this components work together are shown below.
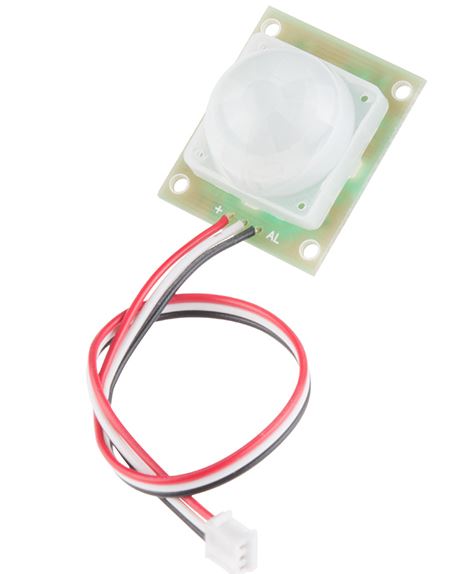
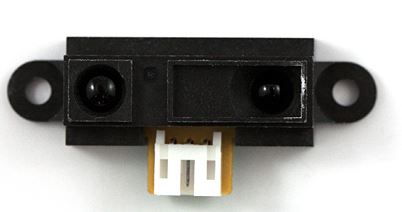
Software Design
In order to accomplish the task given from a customer to implement a system under which observations could be done at multiple times to check upon incoming sources, the following guide will provide the privilege of describing the functionality with basic functions.
Part one distance sensing units: In order to make a fully functional embedded system the a distance sensor needed to be implemented in order to know how long the source was away from the origin. Our device makes fully functionality use of the analog to digital converter in which multiple voltage steps are measured to transfer an analog voltage that is created from a led source inside the device that will bounce off white spots and be seen as a digital converter on a microprocessor unit.
Part two motion sensing unit : By making full use of the pir sensor that was bought in adrafuit.com, the motion sensor enabled us to recognize if a source was approaching. As shown in the block diagram, the way under which the device functions is that it returns a boolean voltage value as kinetic energy is sensed.
Part three display: In order to output a signal or a reference of the status of sources, two 8x8 leds were used. The method in software under which they behaved hold on a users actions. If detection was done two acting eyes would appear and measure the distance, otherwise eyes would be closed. In the source files we are able to observe the use of serial peripherical interface in order to clock in data to these devices as status signals provided feedback to the system.
Implementation
This section includes implementation, but again, not the details, just the high level. For example, you can list the steps it takes to communicate over a sensor, or the steps needed to write a page of memory onto SPI Flash. You can include sub-sections for each of your component implementation.
Testing & Technical Challenges
The first thing that we would tell ourselves if we were able to go back in time is to buy better devices. The sensors that we bought are really sensible and have delays and other problems that lead to obtaining the wrong outcome or the receive the outcome at different unexpected times. We notice this when testing. Our first test we did was the first time we were going to use the motion sensor in a while after having it tested a few weeks after it had arrived. We notice that it didn't work and it wasn't until we found out that sensor has an extra delay that makes the sensor take more then 40 seconds for it to start working properly. Also, the pins for the distance sensor are really sensitive and don't stay put. We notice this since it would sometimes measure the correct distance and a second later it will be negative. In addition, one they actually work, we did multiple test by moving our hands at different distances from both sensors. When we notice that it actually work, we installed the servo which we had been able to make it work by itself. However, we had to take it off from a few of the test that we had, ended up making MENL become FMENL, (flying monster encounter night light). Then, we retested everything again the night previous to the presentation, and notice that the distance sensor wasn't able to actually produce the night light since it kept detecting that there was something in front of it, when there was nothing at all.
My Issue #1
We couldnt get the LCD Display to work. It seem to be a manufacturing problem, and it was too late to replace it so we drop it from the project.
My Issue #2
The servo seem to from time to time, not want to stop, this lead to wire wrapping problems and parts just flying away, so we decided to take it away. It was meant to make MENL rotate so it can look for other objects.
Conclusion
Conclude your project here. You can recap your testing and problems. You should address the "so what" part here to indicate what you ultimately learnt from this project. How has this project increased your knowledge?
Project Video
Upload a video of your project and post the link here.
https://www.youtube.com/watch?v=Bbh2tejiG7Y&feature=youtu.be
Project Source Code
References
Acknowledgement
We would like to Ann Verakukala for providing us with one of the LED Matrices. Second we would like to thank all of the cmpe 146 personnel and students, they help us shape our projects to become MENL over other ideas that we had on mind.
References Used
We made all of our code with the libraries provided by FreeRtos and Drivers created from previous labs projects.
Appendix
- PIR Motion Sensor (JST) Datasheet: https://www.sparkfun.com/datasheets/Sensors/Proximity/SE-10.pdf
- MOD-LED8x8RGB schematics: https://www.olimex.com/Products/Modules/LED/MOD-LED8x8RGB/resources/MOD-LED8x8RGB_Rev_B1_sch.pdf
- Infrared Proximity Sensor - Sharp GP2Y0A21YK : https://www.sparkfun.com/datasheets/Components/GP2Y0A21YK.pdf
- The CMPE 146 wiki page